The First-Ever Glock Factory Tour
Major Pandemic 03.07.17
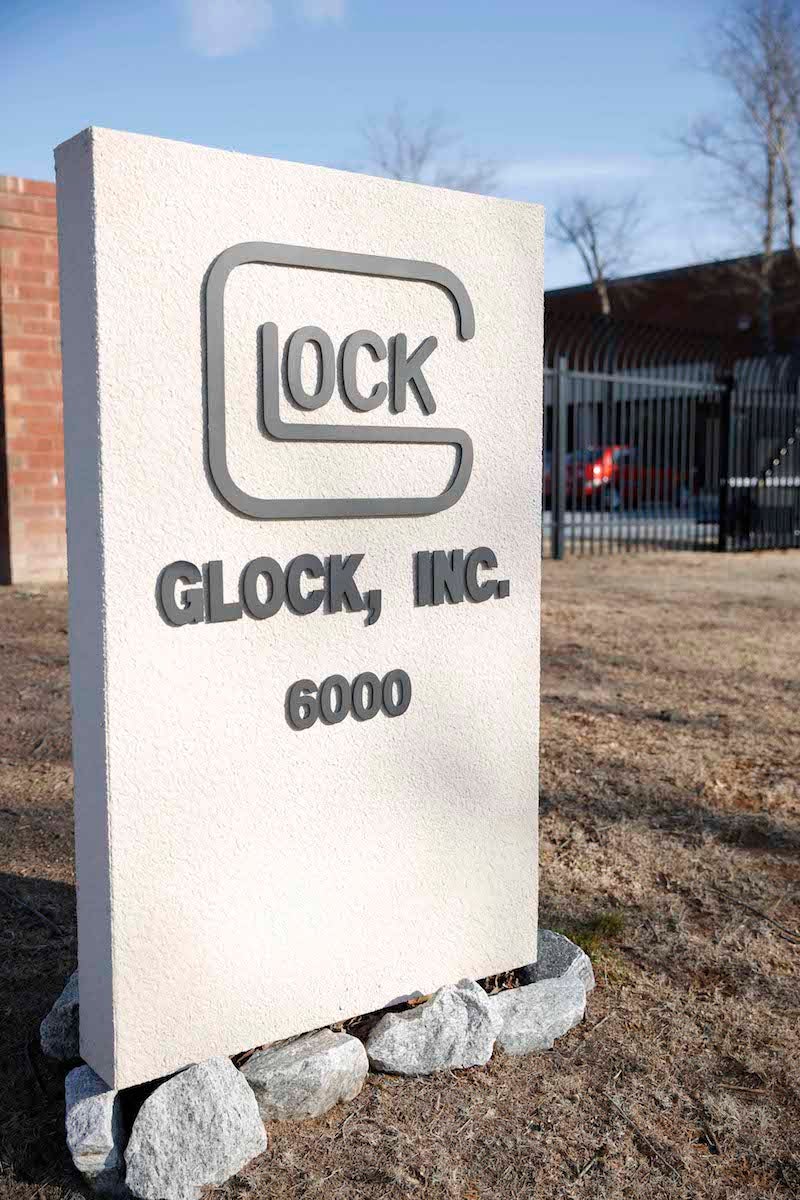
Glock has never been particularly “open” with the media. In fact, for the most part their media engagement has been downright cold, and their approach to media relations feels like a strict and emotionally-distant parent who gives you what you need versus what you want.
For example, shooters asked for a single stack 9mm and we end up with the G42 380 ACP power pistol which is not what we asked for but what the market clearly needed. Of course the G43 finally followed. We ask for a Glock carbine and we get new competition guns precut for reflex sights.
And the list goes on. So I was surprised when Glock invited me to an exclusive small group tour of the Glock facilities and US production factory in Smyrna Georgia. Before I take you along on the tour, readers must understand the colorful background of the event and what felt like a weird, socially uncomfortable, amazingly wonderful, Willy Wonka tour experience.
There were only eleven writers invited this factory tour event. I did not really understand how small and exclusive the group was until Mike Robinson, head of Glock marketing (2015), and I bumped into each other at the hotel before the kickoff dinner. Without Mr Robinson maintaining levity, some humor, and ensuring we had a interesting and comfortable visit, I fear this first tour would have felt more like a tour through a supermax prison.
Mike – “Good to see you, everyone is pretty much here. I just bumped into Massad.
Me – “Massad?”
Mike – “Yeah, Massad Ayoob.”
Me – “Are you kidding me? You have that class of legendary writer talent and you invited MajorPandemic.com… what the hell is wrong with you?”
Mike – “Glock likes your unique perspective. Glock is a bit unique so it’s a good fit.”
Me – “How many people were invited?”
Mike – “A dozen but only eleven could make it.”
Me – “I really think you made a mistake, but whatever… let’s get some drinks.”
Massad was not the only top-tier writer, and then there was me. It was a small group, but the event was at least a starting point for Glock, which has previously held secrecy similar to the Wizard of Oz.
We were informed we didn’t need to concern ourselves with taking pictures, because Glock already had pre-approved factory images. Also we would have to sign a non-disclosure agreement (NDA) and commit to not sneaking any pictures during the tour. Cough [control freaks].
You could tell this editorial tour was something everyone at Glock wanted to do, but felt uncomfortable to them. Kinda like after a first date when one person goes in for a kiss and the other person (Glock) just gives a lukewarm hug instead but then wants to just sit on the steps and talk for hours.
Most conversations with Glock start with paperwork and this factory tour started there at the security station where general privacy NDAs were completed, and then we went inside and signed another tour specific NDA, a proposed new product NDA for the yet to be release G43, and a liability waiver if we wanted to shoot any of the factory test guns. Twenty minutes of reading and four yards of ink later the tour began.
To be up-front and possibly disappoint other writers, this was actually my second time behind the closed doors of Glock, but all I saw last time was the inside of Mike’s rather un-impressive office. Glock was then bursting at its seams and needed more building space.
Fast forward two years and Glock has made enormous strides toward that goal with an entire building expansion and makeover. They are still struggling with business growth outpacing their ability to expand. Many divisions are working out of mobile office trailers due to the space limitations.
The inside of Glock had been transformed from a rather dumpy depressing office building two years ago to a floor to ceiling beautifully remodeled building in which anyone would be proud to work.
On to the Factory
Entering the US Manufacturing factory floor, you are greeted with a clean spacious floor plan. I honestly felt like I should remove my shoes because I might get the floor dirty. The sanitized facility achieved what I previously thought to be an unattainable level of cleanliness and organization for a manufacturing facility. Actually it was at a level of OCD organization where everything was excessively labeled and organized.
It’s important to understand that Glock is a paranoid level of “control freak” I had never seen before. For example, they have their own electron microscope and metallurgy department on site to retest and re-certify steels that have already been approved and certified by Glock Austria.
Glock makes their own tools, bits, tooling, mills, dies, etc out of their own certified steel. They even track each serialized tool for wear, so if an endmill wears slightly faster than it should, they can track the source material.
Yep, Glock certifies its own steel, which is used to make the tools, which make the tools, which create the pistols. It’s an unimaginable level of control, all in an attempt to attain Glock Perfection. To take the example of paranoid control even further, I noticed that the tool holders were actually Glock injection-molded parts with a Glock logo. They don’t even trust someone else’s tool holder for the tools they make. The Glock manufacturing goal is to address anything which could create a problem so that there are no problems whatsoever.
When Glock created the US manufacturing facility, they wanted to replicate the Austrian operations, so they did. Not kind of, but exactly. Everything is the same, from the rather common-looking parts bins to the CNC, forging, and injection molding machines and even the shipping boxes.
When their lead manufacturing managers are sent to training in Austria, they can walk back into the US facility and run any of the machines or processes with the same equipment, floor plan, and programs used in Austria. They share every possible measurable statistic between the facilities, from tool wear to manufacturing volumes. When one facility or another updates a process or program, both are updated, then checked, monitored, and measured. Glock US is tightly tethered to the “mothership” in Austria. For this reason, you can rest assured that there is no measurable difference between a Glock pistol made in Austria or in the USA. All use the same materials, processes, and tooling.
Although I have seen plenty of manufacturing robots, Glock’s machine which was molding G42 frames was mesmerizing to watch. Glock has machine automated as many processes as possible.
The barrels, slides, frames, and cases can all be made in the US, and finishing and coating is completed in special in-house operations. Although the remaining internal parts and magazines are still made in Austria, the equipment to make these parts is available in the US should the need arise.
A large percentage of Glocks sold in the US are still made in Austria. All models can technically be made in the US facility, but currently only a small percentage of legacy Glock models are made in the US. During our tour, Glock was cranking out G42 models in the Smyrna facility at a blistering rate. Glock explained that Austria manufactures the bulk of the overall production and can absorb the sales peaks and fulfill unexpected demand.
One particular response I received regarding tool wear was that Glock does not follow an 80% tool-wear replacement plan like most manufacturers. Generally a tool is replaced at its 80% service life point, but Glock notes that they test each tool after every single machining cycle, digitally record and track that wear, and then replace it only after a particular wear pattern emerges, which may occur at 62% or 99% service life. Glock’s drive for perfection may seem extreme but they have assured total internal control for every aspect of the Glock pistol manufacturing process is as perfect as possible.
If Glock was a girlfriend she would have already statistically calculated and predictively modeled everything including dinners for the next forty-five years, the exact proposal and marriage dates, and number of children you will have all before you would have even met for the first time at Church. Your life would be Glock Perfection with a gal who may not be the prettiest but she would rock your world with everything you never imagined you needed in a woman.
The tour concluded with the pre-release and hands-on testing of the “super secret” G43 9mm single stack pistol. The development and release of the G43 was so predictable that every writer in the room was saddened a bit when it was the only reveal. I asked, “Are you sure you’re not coming out with a 22LR G42-LR or something, because the G43 is not really a surprise?”
Every writer present was happy that Glock had finally unveiled the G43, but we were happier that Glock had finally broken its silence and allowed us into their wonderfully strange world which is masterfully designed to do just one thing: deliver GLOCK PERFECTION.
That weird quirky first date that Glock provided in the first-ever factory tour made me love Glocks even more, because I have seen for myself how they put their minds, heart, and souls into ensuring they produce the best possible product.